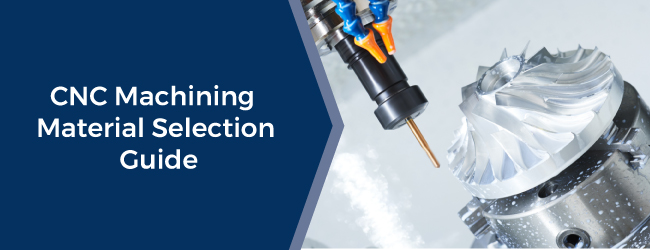
Jump to:
- Essential Questions for Selecting the Right CNC Material
- High Temperatures and Their Impact on Materials
- Material Selection for Manufacturing
- Environmental Considerations
- General Tips on CNC Machining Certain Materials
- Contact American Micro Industries to Discuss CNC Machining Materials
CNC machining has become a staple for a wide array of disciplines that need specialized parts manufactured for their projects. CNC materials have expanded to meet the demands of consumers, engineers, contractors and other fields to create solutions for very specific applications. Having a variety of materials to choose from is a luxury, but it can also be overwhelming and confusing if you don’t analyze what your needs are and ask yourself some questions before making a decision.
Our guide to CNC machine material selection can help you find suitable products to ensure efficiency and excellent results. This guide will walk you through the following steps so you can choose ideal CNC materials for your project:
- Defining how the product you’ll make will be used so you can base your material decisions on end-result functionality
- Analyzing whether your product will be used indoors, away from harsh weather, or outdoors, where it may need corrosion-resistant properties
- Determining the material’s necessary stress load and dimensional tolerance so you can create a reliable product based on its projected use
- Considering whether your part will need compatible fasteners or have wear resistance properties so it can be a fastener itself
- Knowing the product’s ideal operating temperatures so you can choose a material that can withstand necessary temperature changes
- Gauging your product’s weight and stress capacity to choose the material that will let your part function properly
- Calculating your project costs to ensure you get a good deal for the material you choose
Essential Questions for Selecting the Right CNC Material
Choosing the right materials for your part is the difference between mediocre outcomes and optimum results. These important questions are the best place to start. The more you can narrow down the CNC materials that would be the best fit for your part, the easier it will be to select a material that will suit your needs and be cost-efficient. Here are some things you should consider.
Learn About Our CNC Machining Services
Properties of Materials in CNC Machining
First and foremost, you must consider how you will be using the part and whether your application involves indoor or outdoor environments. Outdoor and indoor environments are very different — one completely depends on the weather, whereas the other is usually a much more controlled environment.
For instance, in outdoor environments, you need to plan for moisture. Your material will need to be able to resist the effects of corrosion, such as rusting, in order to maintain its integrity over time. Rigid foam provides a great example of a material that resists moisture and rusting while also maintaining structural integrity.
Extreme temperatures, both high and low, will also eliminate certain materials as the best option. You may also need to meet code for FDA-regulated specifications. Where you will store your products and how they react to moisture and extreme temperature changes become a cornerstone in deciding which material to use.
Stress and Load Considerations
High-stress loads can cause certain materials to strain or even break. When you’re considering which material to use for your part, make sure you’ve accounted for stress load. If your part will be exposed to high stress, the material it’s made of will need the ability to resist loads and prevent deformation.
Dimensional Tolerance
When you’re considering CNC-machined components, pay close attention to dimensional tolerance. In addition to impacting the success of your manufacturing process, dimensional tolerance also affects your bottom line, the parts and tools you choose and their assemblies and cutting methods.
You need to know the tolerance necessary for your part. If you’re working from an old part design or sketch, it’s a good idea to make sure the tolerance is appropriate. Typos can easily occur in documentation. Even if the information is correct, if you can make an adjustment to loosen the tolerance and still allow the part to work to its full potential, you could save money by re-evaluating tolerance. Tighter tolerances are often more expensive to produce.
Some machining tools use a standard dimensional tolerance as a default, but if you don’t specify a tolerance or discover that your numbers are off, you’ll end up ordering a part that may not fit or work at all. While you can fix this, it will take more time out of your project to resize or reorder the part, which can end up costing you more than if you had determined the correct tolerance upfront. This simple initial step can help you save money in the long run.
If you aren’t sure what the exact tolerance is for the part you need, instead of risking a guess, let a CNC machining company like American Micro Industries help you figure it out.
Learn About Our CNC Machining Services
Cost Analysis
The most expensive materials are usually high-strength, lightweight materials. The best method for choosing a cost-effective component is selecting one that meets your strength profile, temperature restrictions and fitment requirements. The more crucial requirements or restrictions you have for your materials, the easier it will be to focus on those key elements.
Finding an industry that provides free quotes and no minimum for your materials will help cut costs right off the bat. Once you narrow your details, you can decide on a more cost-efficient material that meets most of your needs.
High Temperatures and Their Impact on Materials
High temperatures play a crucial role when selecting what materials to use, as many materials will deteriorate under extreme heat. A popular plastic that loses strength under high temperatures is polyvinyl chloride, or PVC. While it has a good fire resistance rating, its working temperature is about 176° F. Stability tends to be lost around 280° F, making it unfit for some projects.
Some materials are resilient and durable under these high-heat conditions. For example, polyisocyanurate has properties that do not allow it to melt or freeze. The thermoset plastic is processed as a viscous material first, allowing it to form multiple shapes. After curing, it becomes rigid and exceptionally stable. When you’re wondering what materials you can use in a CNC machine to create the part you need, make sure you consider how the material handles high temperatures.
What Are the Weight and Stress Capacities?
Depending on what you want to do with your CNC–machined components, you should consider the weight of your materials. Bigger isn’t always better, and less doesn’t always mean more — especially when it comes down to cost.
Heavy materials absorb a great deal of stress. For projects that require excessive weight–bearing capabilities and resistance to high-stress loads, you may consider heavy materials. If you work on weight-sensitive projects, however, you might want to avoid heavy materials.
Lightweight materials are popular for weight-sensitive projects. While they are not as hefty as heavy materials, they still are durable and able to absorb a substantial amount of stress. Unfortunately, they are not very cost-effective, as they usually won’t include every material feature desired for your project. Lightweight materials are ideal for a number of products, but if cost is an important factor, they might not be a good fit.
Choosing between heavy and lightweight materials is just one reason why it’s important to prioritize the most important characteristics of your CNC-machined part. That way, you can specify what elements are crucial for your part in order for it to function properly, eliminate materials that don’t meet those standards and then compare costs.
Learn About Our CNC Machining Services
Other Durability Factors to Consider
Strength doesn’t necessarily mean how much weight an object can withstand. There are more components that you may need to examine, such as:
- Tensile strength: An object’s resistance to breaking under tension.
- Endurance strength: An object’s overall stress absorption capacity.
- Wear resistance: An object’s ability to handle friction or be self-lubricating. A good example of this is Ultra High Molecular Weight (UHMW) polyethylene. It’s a similar product to Teflon®, but it is more abrasion-resistant.
- Hardness: An object’s ability to withstand pinpoint surface loads. Hardness is usually indicated with a Brinell or Rockwell hardness number.
Material Compatibility
If you’re having a challenging time determining the right material, a better question might actually be what materials you cannot use. CNC machines cut through nearly any material you can think of. While you can use a wide range of materials in a CNC machine, the most commonly employed materials used are:
- Metals: Steel, brass or aluminum
- Plastics: Polypropylene (PP), acetal (POM), polycarbonate (PC) or acrylics (PMMA)
- Foam: Carving foam and rigid foam
Material Selection for Manufacturing
CNC machining has increased in popularity because it delivers high precision for demanding industries and empowers teams to meet production demands. With so many material choices on the market, choosing the right one can take time and several rounds of trial and error. Every material is different and can bring unique benefits or drawbacks to your applications. Often, you may find that several materials seem like a good fit for your projects. Understanding the materials available and their ability to meet requirements or uphold standards can help you decide which ones to test to find the best fit.
What Type of Material Should You Try?
Once you’ve considered all of the factors listed above, chances are you’ll be able to determine which material is the best fit for your part. You may need to experiment with several material types to find the most suitable choice. Here’s an overview of four popular materials used in CNC-machined components:
- Rigid foam: Rigid foam can perform in low temperatures down to -100° F and high temperatures up to 200° F. Rigid foam has a high R-value, making it a premium choice for structure-based products like walls and floors that must insulate well.
- Carving foam: Carving foam applications often include acting as models for molds because this material can take on nearly any shape. Carving foam is flexible but also offers uses in components such as gaskets and seals because it contains dense and resistant polyisocyanurate.
- Phenolics: When meeting military-grade specifications such as MIL-I-24768 is a requirement, phenolics are the ideal choice. You can select from G7, G11, G9, G10/FR4, G10, LE and CE for various capabilities and strengths. For example, phenolic lines possess good mechanical properties and dimensional stability to deliver an excellent finish for machined components compared to CE materials. LE phenolics meet MIL-I-24768/13 FBE requirements, while CE phenolics meet MIL-I-24768/14 FBG requirements. However, you should not use this material for electrical primary insulation.
- Plastics: Many types of plastics are available, typically suitable for electrical insulation, bushings or bearings. However, there is a market for other popular plastics because the material offers a broad range of uses and delivers benefits across industries, including electronics, medical, aerospace and automotive.
Learn About Our CNC Machining Services
Industry Standards and Material Grades
Every sector must meet unique demands, adhere to specific regulations and uphold industry standards. Material grades and industry standards are essential for quality assurance and ensuring compatibility for specific applications. Recognizing these standards and the material grades that satisfy these requirements can point you in the right direction for the materials you need. Some standards to note include:
- International Organization for Standardization (ISO): ISO 9001 is a globally recognized standard that guides teams to improve quality and performance.
- American Society for Testing and Materials (ASTM): These standards depict requirements for material specifications, performance criteria and testing methods. For example, ASTM A36 relates to structural steel, and ASTM D635 provides plastic insights.
- American Society of Mechanical Engineers (ASME): The ASME Y14.5 standard establishes requirements, recommended practices and related information for engineering documents and similar documents. ASME B46.1 outlines information for surface texture relevant to manufacturing, production, drafting and design.
- Society of Automotive Engineers (SAE): Automotive and aerospace sectors adhere to SAE standards regarding metal and composite specifications. For instance, SAE J403 provides information regarding steel grades and the limits and ranges for various carbon steels.
Environmental Considerations
For many teams, environmental considerations will be a significant indicator of ideal CNC machining materials, both in terms of the operating environment and the impact a material has on the environment. Some materials can withstand extreme environments, while others may offer superior resistance to elements like moisture or heat. Teams looking for more sustainable processes may benefit from selecting materials that are reusable or have low environmental impact.
What Are the Operating Temperatures?
Consider the operating temperature the part will need to withstand when it’s in place as a part of your manufacturing process. You want to be sure the melting point of the material you choose is lower than that of the operating temperature. You also want to ensure the material can handle operating temperature changes. While some of the more durable materials are built to withstand these changes, many will show signs of warping, expansion or breakdown over time. Extreme temperatures can also negatively impact the durability of some materials.
Operating temperature is equally as important to know when you’re using CNC machining materials, so you can be sure the temperatures that result from the cutting and shaping of the part will not distort it. Making the connection between the operating temperature and the material you’re using is essential to a successful design and production run.
What Is the Required Fastening?
If you’re going to use the CNC-machined components as fasteners, consider that as you choose a material. Materials influence how securely fasteners will fit together. Different materials have different properties — for example, strength, corrosion resistance, brittleness and galvanic corrosion — so you should choose a material that reflects the properties you want your fasteners to have. The most common material for fasteners is steel, but you can also create quality fasteners from other materials.
If you’re searching for a new part to fasten, it needs to fit perfectly. If you fail to consider the type of fastening you’ll need when you’re deciding on a material, your mechanism may not function properly.
What Are Sustainable Material Choices?
As sustainability continues to be a driving factor in many consumer choices, teams across industries are becoming more concerned with finding sustainable materials and practices. Thankfully, there are several opportunities to lower your environmental impact with the right materials for CNC machining.
For example, recycled aluminum or steel are excellent options for sustainability. Advanced high-temperature alloys can also present unique opportunities for CNC machining while lowering environmental impact. Additionally, you can look for biodegradable plastics to embrace this material’s versatility while highlighting your commitment to the environment.
Learn About Our CNC Machining Services
General Tips on CNC Machining Certain Materials
The decision of which of the CNC machining materials to use for your part ultimately depends on what you’re looking to create, but here are some general tips to use as a brief CNC materials guide:
- Consider non-metallic materials: Don’t assume metals are your best option. Non-metallic materials have become popular because they are lightweight yet durable — like foam you can mold into various shapes. Non-metals also retain small details during cutting. If your project seems like one that may benefit from the use of non-metals, plenty of options can benefit your final product.
- Know the difference between foams: Remember that rigid foam and carving foam serve different purposes. While both are lightweight, yet durable, rigid foam is best for parts with a focus on structural integrity and stability, while carving foam is often used as insulation and prototypes for molds.
- Consider phenolics: Phenolics are great options, especially when you need to adhere to specific regulations or specifications for military-related projects.
- Learn about different plastics: You can choose from a wide variety of diverse plastics. Acetal is often used for bushing and bearing replacements. Polyvinylidene fluoride polymer (PVDF) is used in insulation for electrical wiring. You can employ UHMW in medical biomaterials, such as knee, hip and spine replacement devices. These are just a few examples of the endless possibilities offered by plastics.
Contact American Micro Industries to Discuss CNC Machining Materials
Finding the right CNC machining materials involves considering your application and the various needs you must meet. It also involves finding a reliable provider you trust to deliver high-quality products. Ask yourself what type of company you want to work with to machine your materials. Look for turnkey industries with strong attention to detail and the ability to create hard-to-find parts. Do your research and select your company based on values, quality and efficiency as well. American Micro Industries offers the solutions you need in a timely and affordable fashion.
American Micro Industries has decades of experience manufacturing made-to-order components and parts for various industries. We strive to exceed customer satisfaction and expectations, and our quality-focused and customer-oriented operations empower us to do just that.
We want to help you find the necessary parts to meet the strictest quality standards and enhance operations. This guide should provide some insight and guidance to your decision-making process, but if you need assistance, get in touch with us to discuss any additional concerns about materials or the CNC machining process to clear up any lingering questions you may have. When you are ready to begin, we are ready to assist you.